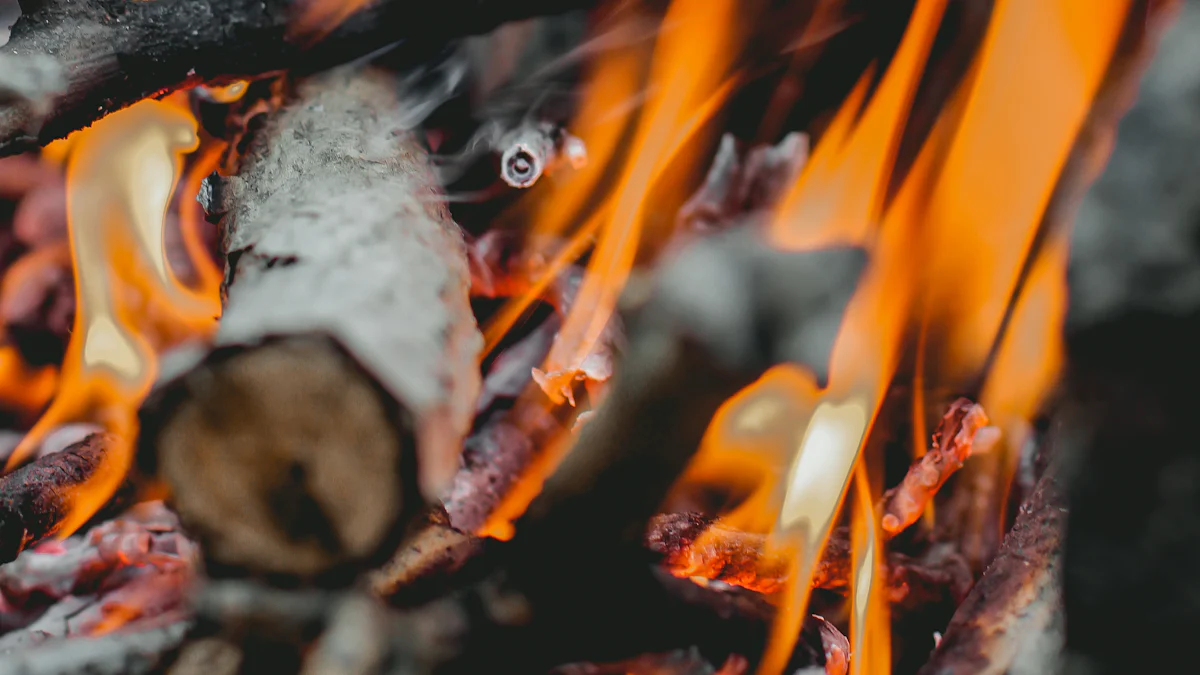
Understanding the causes DTF powder burning during curing is crucial for achieving successful DTF transfers. You might encounter issues like incorrect temperature settings or uneven heat distribution, which can lead to burning. Poor-quality DTF powder and inadequate curing time also contribute to this problem. Recognizing these causes DTF powder ensures that your DTF printing process remains efficient and effective. By mastering the intricacies of DTF transfer film application, you enhance the quality of your transfers and minimize errors. This knowledge empowers you to produce vibrant and durable prints consistently.
Key Takeaways
Maintain optimal temperature settings between 320°F and 350°F to prevent DTF powder from burning during curing.
Regularly calibrate your heat press to ensure consistent heat distribution and avoid uneven curing.
Use high-quality DTF powder with small particle sizes for better adhesion and to minimize the risk of burning.
Monitor humidity levels in your workspace, keeping them between 40% and 60% to prevent moisture-related issues during curing.
Implement routine equipment maintenance to identify and fix potential malfunctions that could lead to uneven heat distribution.
Test different curing times based on your specific setup to find the ideal balance between time and temperature for optimal results.
Utilize heat-resistant mats to promote even heat distribution and enhance the quality of your DTF transfers.
Incorrect Temperature Settings
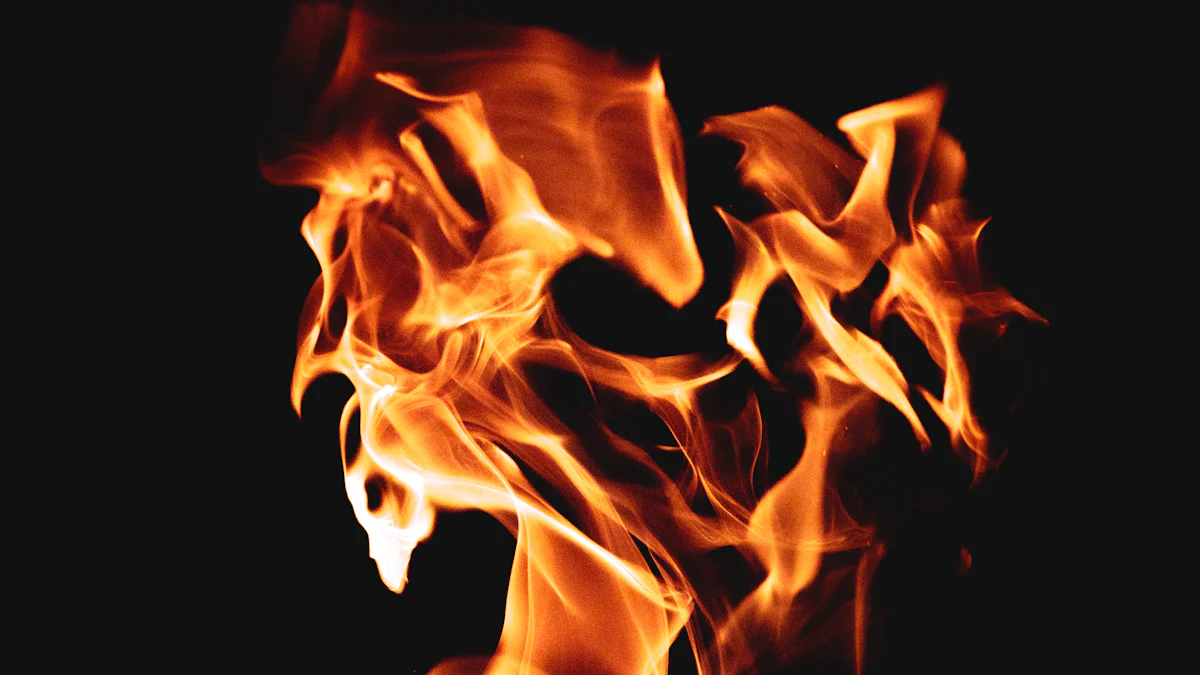
Understanding the correct temperature settings is crucial for successful DTF transfers. Incorrect temperature settings can lead to burning, which affects the quality of your prints. Let’s delve into how you can manage these settings effectively.
Understanding Optimal Temperature
Recommended Temperature Ranges
For optimal results, you should cure DTF powder within a specific temperature range. Generally, the recommended temperature for curing DTF powder is between 320°F and 350°F. This range ensures that the powder adheres properly without burning. Always refer to the manufacturer’s instructions for precise temperature guidelines, as different powders may require slight adjustments.
Effects of High Temperatures
Exposing DTF powder to excessively high temperatures can cause it to burn. This not only ruins the print but also damages the material. High temperatures can lead to uneven curing, resulting in poor-quality transfers. Therefore, maintaining the recommended temperature range is essential to avoid these issues.
Adjusting Heat Press Settings
Properly adjusting your heat press settings is vital for achieving the desired results in DTF transfers.
Calibrating Your Equipment
Calibration of your heat press ensures that it operates at the correct temperature. Regular calibration checks help maintain consistent heat distribution, preventing any potential burning of the DTF powder. You should follow the manufacturer’s guidelines to calibrate your equipment accurately.
Monitoring Temperature Consistently
Consistent monitoring of the temperature during the curing process is crucial. Use a reliable thermometer to check the heat levels regularly. This practice helps you detect any fluctuations that might lead to burning. By keeping a close eye on the temperature, you ensure that your DTF transfers are both vibrant and durable.
Uneven Heat Distribution
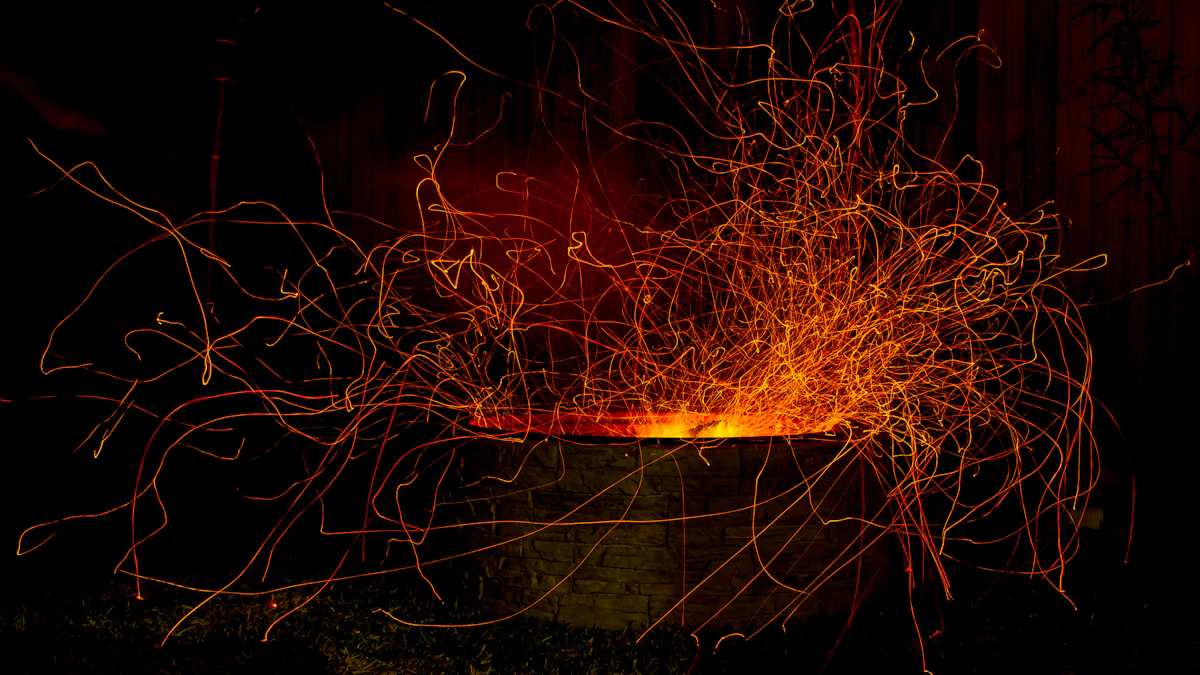
Uneven heat distribution during the curing process can significantly impact the quality of your DTF prints. Addressing this issue ensures that your transfers are vibrant and durable.
Causes of Uneven Heat
Equipment Malfunctions
Equipment malfunctions often lead to uneven heat distribution. When your heat press or other curing equipment fails to operate correctly, it can create hot and cold spots on the surface. These inconsistencies result in some areas of the DTF powder burning while others remain uncured. Regularly inspect your equipment for any signs of wear or damage to prevent these issues.
Inconsistent Pressure Application
Inconsistent pressure application also contributes to uneven heat distribution. If the pressure applied during the curing process varies across the surface, it can cause certain sections to receive more heat than others. This inconsistency can lead to uneven curing and potential burning of the DTF powder. Ensure that you apply uniform pressure throughout the process to achieve consistent results.
Solutions for Even Heat
Regular Equipment Maintenance
Regular maintenance of your curing equipment is essential for ensuring even heat distribution. By keeping your equipment in optimal condition, you minimize the risk of malfunctions that could lead to uneven heating. Follow the manufacturer’s maintenance guidelines and schedule routine checks to keep your equipment running smoothly.
Using Heat-Resistant Mats
Heat-resistant mats can help distribute heat evenly during the curing process. These mats act as a buffer, ensuring that the heat spreads uniformly across the surface. By using heat-resistant mats, you reduce the likelihood of hot spots and improve the overall quality of your DTF transfers. Incorporate these mats into your setup to enhance the consistency of your prints.
Poor-Quality DTF Powder
Selecting the right DTF powder is crucial for achieving high-quality prints and ensuring the durability of your transfers. Poor-quality powder can lead to several issues, including burning during the curing process. Understanding the characteristics of good powder and recognizing trusted brands can help you make informed decisions.
Identifying Quality Powder
Characteristics of Good Powder
High-quality DTF powder typically features small particle sizes, ranging from 50 to 100 microns. This fine texture offers a smooth finish and enhanced clarity, making it ideal for intricate designs. When you choose powder with these characteristics, you ensure that your prints are precise and detailed. Additionally, good powder should provide vibrant colors and be versatile enough for various fabric applications.
Trusted Brands and Suppliers
To ensure the quality of your DTF printing, it’s essential to source powder from reputable brands and suppliers. Trusted brands often offer powders that are stretch-resistant, waterproof, and suitable for both light and dark-colored garments. By choosing reliable suppliers, you minimize the risk of encountering low-quality products that could compromise your print quality and transfer durability.
Consequences of Using Low-Quality Powder
Increased Risk of Burning
Using low-quality DTF powder significantly increases the risk of burning during the curing process. Inferior powders may not withstand the recommended temperature ranges, leading to uneven curing and potential damage to the material. This not only affects the appearance of your prints but also reduces their overall durability.
Impact on Print Quality
The quality of your DTF transfer film directly influences the final print outcome. Low-quality powder can result in poor adhesion, causing the prints to peel or crack over time. This compromises the transfer durability and diminishes the vibrancy of the colors. To maintain high standards in your DTF projects, always prioritize quality powder that guarantees excellent print results and long-lasting durability.
Inadequate Curing Time
Inadequate curing time can significantly affect the quality of your DTF prints. Understanding the right duration for curing ensures that your transfers are both vibrant and durable. Let’s explore how you can determine the optimal curing time and balance it with temperature for the best results.
Determining Proper Curing Time
Factors Influencing Curing Duration
Several factors influence the curing time for DTF powder. The type of powder you use plays a crucial role. Different powders may require varying durations to achieve proper adhesion. The temperature of your heat press also affects the curing process. Higher temperatures might reduce the time needed, while lower temperatures could extend it. Additionally, the thickness of the powder layer impacts the curing time. Thicker layers generally require more time to cure thoroughly.
Testing for Optimal Results
To achieve the best results, you should test different curing times. Start by following the manufacturer’s recommendations, which typically suggest curing DTF powder for 2-3 minutes at 325 degrees Fahrenheit (160 degrees Celsius). Adjust the time based on your observations. If the powder doesn’t adhere well, increase the duration slightly. Conversely, if you notice burning or discoloration, reduce the time. Consistent testing helps you find the sweet spot for your specific setup.
Balancing Time and Temperature
Avoiding Over-Curing
Over-curing can lead to adhesion problems and damage your prints. When you expose DTF powder to excessive heat for too long, it may cause the powder to burn or the colors to fade. To avoid this, ensure that you monitor both the time and temperature closely. Use a timer to keep track of the curing duration and adjust the heat press settings as needed.
Ensuring Complete Adhesion
Achieving complete adhesion is essential for durable DTF transfers. Proper curing ensures that the powder melts and bonds effectively with the ink and film. This process enhances the durability and brightness of your prints. By balancing the curing time and temperature, you minimize the risk of adhesion problems and produce high-quality transfers consistently.
Environmental Factors
Environmental factors play a significant role in the success of your DTF printing process. Understanding how humidity, airflow, and temperature variations affect curing can help you achieve optimal results.
Impact of Humidity and Airflow
Humidity and airflow can greatly influence the curing process of DTF powder. Managing these elements ensures that your prints remain vibrant and durable.
Controlling Humidity Levels
You should maintain an ideal humidity level in your workspace to prevent issues during the curing process. High humidity can cause the DTF powder to absorb moisture, leading to uneven curing and potential burning. Aim to keep the humidity between 40% and 60% for optimal results. Using a dehumidifier can help you control moisture levels effectively, ensuring that your DTF transfers adhere properly and maintain their quality.
Ensuring Proper Ventilation
Proper ventilation is crucial for maintaining consistent airflow during the curing process. Good airflow helps regulate temperature and prevents the accumulation of excess heat, which can lead to burning. Ensure that your workspace has adequate ventilation by using fans or opening windows. This practice not only aids in even curing but also enhances the overall safety of your working environment.
Temperature Fluctuations
Temperature fluctuations can impact the quality of your DTF prints. Maintaining a stable environment helps you achieve consistent results.
Maintaining a Stable Environment
You should strive to keep the ambient temperature in your workspace between 68°F and 75°F. This range provides the best conditions for DTF printing, ensuring that the powder cures evenly and adheres well. Sudden changes in temperature can cause the powder to burn or fail to cure properly. By monitoring and adjusting the temperature, you can minimize these risks and produce high-quality prints consistently.
Using Climate Control Solutions
Implementing climate control solutions can help you manage temperature variations effectively. Consider using air conditioning or heating systems to maintain a stable environment. These solutions allow you to control the temperature precisely, reducing the likelihood of issues during the curing process. By investing in climate control, you enhance the reliability and quality of your DTF transfers.
Incorrect Application Techniques
Mastering the application techniques in DTF printing is essential for achieving high-quality results. Mistakes during application can lead to issues such as misalignment and inconsistent pressure, which affect the final print quality. By understanding these common errors and adopting best practices, you can enhance your DTF printing process.
Common Mistakes in Application
Misalignment of Film
Misalignment of the film is a frequent error in DTF printing. When the film is not properly aligned, it can cause the design to shift, resulting in an uneven print. This misalignment often occurs when you rush the setup process or fail to secure the film correctly. To avoid this, take your time to align the film accurately before starting the transfer process. Use alignment tools or guides to ensure precision.
Inconsistent Pressure
Inconsistent pressure during the application process can lead to uneven prints. When the pressure varies across the surface, some areas may not adhere properly, causing parts of the design to peel or crack. This inconsistency often results from improper calibration of the heat press or uneven surface levels. Ensure that your heat press is calibrated correctly and apply uniform pressure throughout the process to achieve consistent results.
Best Practices for Application
Step-by-Step Application Guide
Prepare the Surface: Ensure that the surface is clean and free of any debris. A smooth surface helps in achieving better adhesion.
Align the Film: Carefully position the DTF film on the substrate. Use alignment tools to ensure that the design is centered and straight.
Set the Heat Press: Adjust the heat press to the recommended temperature and pressure settings. Refer to the manufacturer’s guidelines for specific instructions.
Apply Even Pressure: Lower the heat press evenly over the film. Maintain consistent pressure throughout the curing process to ensure uniform adhesion.
Cool and Peel: Allow the print to cool before peeling the film. This step helps in setting the design and preventing any smudging or distortion.
Tips for Consistency
Regular Calibration: Regularly calibrate your heat press to maintain consistent pressure and temperature settings. This practice minimizes the risk of errors during the application process.
Use Quality Tools: Invest in high-quality alignment tools and heat-resistant mats. These tools aid in achieving precise alignment and even heat distribution.
Practice and Patience: Practice the application process to improve your skills. Take your time to ensure accuracy and consistency in every print.
By following these best practices, you can minimize errors and enhance the quality of your DTF prints. Consistent application techniques lead to vibrant and durable transfers, ensuring customer satisfaction and professional results.
Preventive Measures and Best Practices
Implementing preventive measures and best practices in your DTF printing process can significantly enhance the quality and durability of your prints. By focusing on regular equipment checks and skill development, you ensure that your DTF transfers remain vibrant and consistent.
Regular Equipment Checks
Routine maintenance of your equipment is crucial for preventing issues that could affect the quality of your DTF prints.
Importance of Routine Maintenance
Regular maintenance keeps your equipment in optimal condition. It helps you identify potential problems before they escalate, ensuring that your DTF printing process runs smoothly. By maintaining your equipment, you reduce the risk of malfunctions that could lead to uneven heat distribution or incorrect temperature settings. This proactive approach not only extends the lifespan of your equipment but also enhances the quality of your prints.
Checklist for Equipment Health
To maintain your equipment effectively, follow a comprehensive checklist:
Inspect Heating Elements: Check for any signs of wear or damage. Replace faulty elements to ensure even heat distribution.
Calibrate Temperature Settings: Regularly calibrate your heat press to maintain accurate temperature levels.
Clean Surfaces: Keep the surfaces of your equipment clean to prevent debris from affecting the transfer process.
Check Pressure Settings: Ensure that the pressure settings are consistent and adjust them as needed.
Test Equipment Functionality: Conduct routine tests to verify that all components are functioning correctly.
By adhering to this checklist, you maintain the health of your equipment and improve the reliability of your DTF transfers.
Training and Skill Development
Investing in training and skill development is essential for mastering DTF printing techniques and achieving professional results.
Importance of Proper Training
Proper training equips you with the knowledge and skills needed to execute DTF printing effectively. It helps you understand the intricacies of the process, from temperature settings to application techniques. With adequate training, you minimize errors and enhance the quality of your prints. This investment in your skills leads to more efficient and successful DTF transfers.
Resources for Learning
To develop your skills, explore various learning resources:
Online Courses: Enroll in courses that cover DTF printing techniques and best practices.
Workshops and Seminars: Attend industry workshops to gain hands-on experience and learn from experts.
Instructional Videos: Watch videos that demonstrate step-by-step processes and offer practical tips.
Industry Publications: Read articles and publications to stay updated on the latest trends and innovations in DTF printing.
By utilizing these resources, you enhance your expertise and ensure that your DTF printing process remains efficient and effective.
Additional Causes of DTF Powder Burning
Understanding the additional causes of DTF powder burning can help you improve your printing process. By addressing these factors, you can ensure that your prints remain vibrant and durable.
Excessive Ink Usage
Excessive ink usage can lead to several issues during the DTF printing process. Managing ink levels effectively is crucial for achieving high-quality prints.
Effects of Micro Boiling
When you use too much ink, it can cause micro boiling during the curing process. This occurs when the excess ink heats up and creates small bubbles. These bubbles can lead to uneven curing and potential burning of the DTF powder. The result is a compromised print quality with visible defects. To avoid this, monitor your ink usage closely and adjust it according to the design requirements.
Managing Ink Levels
Proper management of ink levels is essential for preventing micro boiling. You should calibrate your printer settings to ensure that the right amount of ink is applied. Regularly check the ink levels and adjust them based on the complexity and size of the design. By maintaining optimal ink levels, you reduce the risk of excessive powder burning and enhance the overall quality of your DTF prints.
Moisture in Powder or Garment
Moisture present in the powder or garment can significantly affect the curing process. Identifying and controlling moisture issues is vital for successful DTF transfers.
Identifying Moisture Issues
Detecting moisture issues early can prevent problems during the curing process. You should inspect the DTF powder and garments for any signs of moisture before starting the transfer. Look for clumping in the powder or dampness in the fabric. These indicators suggest that moisture is present and could lead to uneven curing or burning.
Solutions for Moisture Control
Implementing solutions for moisture control can help you achieve consistent results. Store your DTF powder in a dry environment to prevent moisture absorption. Use airtight containers to keep the powder fresh and free from humidity. For garments, ensure they are completely dry before applying the DTF transfer. Consider using a dehumidifier in your workspace to maintain optimal humidity levels. By controlling moisture, you minimize the risk of excessive powder burning and improve the durability of your prints.
Understanding the causes DTF powder burns during curing is essential for successful DTF transfers. You must address each cause, from incorrect temperature settings to poor-quality powder, to prevent burning. Implementing preventive measures like regular equipment checks and proper training enhances your DTF printing process. Always follow the manufacturer’s instructions for specific DTF powder to avoid overheating, which can damage the fabric or print quality. By mastering these aspects, you ensure vibrant and durable transfers, elevating the quality of your work.
FAQ
What is the importance of curing DTF powder?
Curing DTF powder is essential for achieving the best print quality and durability. You need to cure the powder to ensure that it adheres properly to the fabric, resulting in vibrant and long-lasting prints. Most DTF powders require curing for 30 to 60 seconds at temperatures between 320 to 350 degrees Fahrenheit. This process enhances the wash-fastness of your prints, making them more resistant to fading and wear.
What is the recommended temperature range for curing DTF powder with an oven?
When using an oven to cure DTF powder, you should maintain a temperature range of about 320 to 350 degrees Fahrenheit. However, always refer to the manufacturer’s instructions for the specific DTF powder you are using, as the recommended temperature and time may vary. Following these guidelines ensures that the powder cures evenly and adheres properly to the fabric.
How long should you cure DTF powder according to general guidelines?
The general guideline for curing DTF powder is to cure it for 2-3 minutes at 325 degrees Fahrenheit (160 degrees Celsius). The curing time can vary depending on factors such as the type of powder, the heat press temperature, and the thickness of the powder layer. By adhering to these guidelines, you ensure that the powder bonds effectively with the fabric, resulting in high-quality prints.
Why is curing the DTF powder with a heat press considered efficient?
Using a heat press to cure DTF powder is one of the most efficient methods for achieving consistent results. The heat press provides uniform heat and pressure, ensuring that the adhesive cures properly. This process delivers bright, wash-fast prints that maintain their vibrancy over time. By using a heat press, you enhance the reliability and quality of your DTF transfers.
Can you use a regular oven for curing DTF powder?
Yes, you can use a regular oven for curing DTF powder, but you must ensure that it can maintain the recommended temperature range of 320 to 350 degrees Fahrenheit. It’s crucial to monitor the temperature closely to prevent overheating, which can lead to burning. Using an oven requires careful attention to detail to achieve the desired results.
What happens if you don’t cure DTF powder properly?
If you don’t cure DTF powder properly, you risk compromising the quality and durability of your prints. Improper curing can lead to poor adhesion, causing the prints to peel or crack over time. Additionally, the colors may fade quickly, reducing the overall vibrancy of the design. Proper curing is essential for ensuring that your DTF transfers remain vibrant and durable.
How can you ensure even curing of DTF powder?
To ensure even curing of DTF powder, you should use equipment that provides consistent heat and pressure, such as a heat press. Regularly calibrate your equipment to maintain accurate temperature settings. Additionally, consider using heat-resistant mats to distribute heat evenly across the surface. These practices help you achieve uniform curing and high-quality prints.
What are the signs of over-curing DTF powder?
Signs of over-curing DTF powder include discoloration, burning, and reduced adhesion. Over-curing occurs when the powder is exposed to excessive heat for too long, causing it to degrade. To avoid over-curing, monitor the curing time and temperature closely, and adjust your equipment settings as needed. By doing so, you protect the integrity of your prints and ensure their longevity.
How does humidity affect the curing process of DTF powder?
Humidity can significantly impact the curing process of DTF powder. High humidity levels can cause the powder to absorb moisture, leading to uneven curing and potential burning. To control humidity, maintain levels between 40% and 60% in your workspace. Using a dehumidifier can help you manage moisture effectively, ensuring that your DTF transfers adhere properly and maintain their quality.
What preventive measures can you take to avoid DTF powder burning?
To prevent DTF powder from burning, you should regularly check and calibrate your equipment to ensure accurate temperature settings. Use quality DTF powder from reputable suppliers to minimize the risk of burning. Additionally, maintain optimal humidity levels in your workspace and follow the manufacturer’s instructions for curing times and temperatures. By implementing these preventive measures, you enhance the quality and durability of your DTF prints.