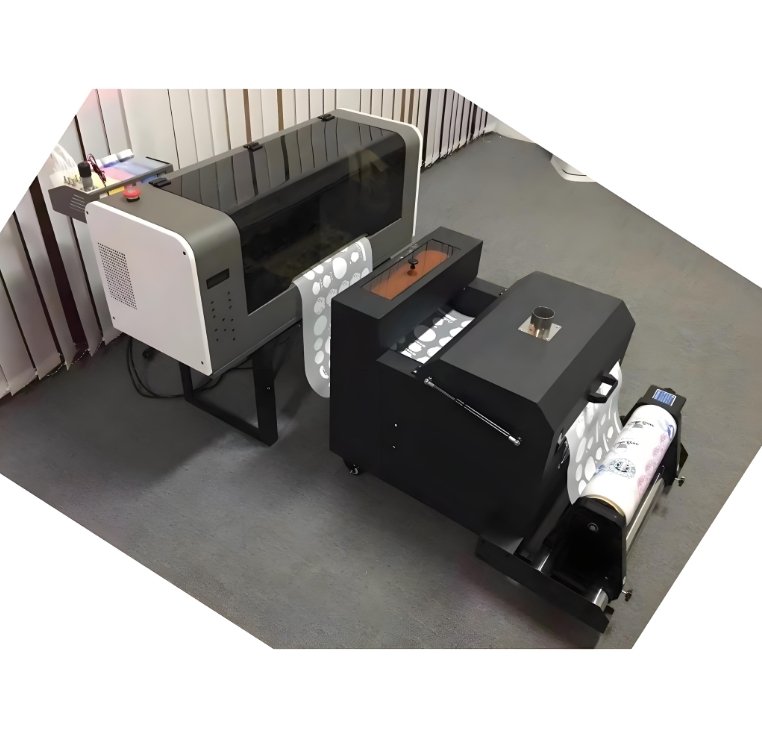
In the world of DTF printing, you often encounter various challenges that can affect the quality of your prints. Understanding these common issues is crucial for achieving successful results. Problems like color inconsistencies, ink adhesion issues, and printhead clogging can significantly impact your work. By learning how to address these challenges, you can ensure vibrant and accurate prints. Regular maintenance and using high-quality materials play a vital role in overcoming these obstacles. With the right knowledge and techniques, you can transform your printing experience and produce exceptional results.
Key Takeaways
Understand the importance of using correct ICC profiles and regularly calibrating your printer to achieve accurate and consistent colors in your DTF prints.
Ensure proper ink adhesion by implementing effective curing techniques and selecting high-quality materials to enhance the durability and appearance of your prints.
Maintain your printhead by establishing regular cleaning routines and using recommended inks to prevent clogging and ensure smooth operation.
Regularly agitate white ink before use to prevent settling and ensure consistent opacity, which is crucial for vibrant designs.
Create a controlled printing environment by managing temperature and humidity levels to avoid issues like smudging and poor ink adhesion.
Follow preventive maintenance practices, such as scheduled cleaning and using maintenance kits, to extend the life of your DTF printer and maintain print quality.
Stay informed about common DTF printing challenges and their solutions to enhance your printing experience and produce exceptional results.
Color Management and Inconsistencies
In DTF printing, achieving accurate and consistent colors can be challenging. Understanding the causes of color inconsistencies and implementing effective solutions is essential for producing high-quality prints.
Causes of Color Inconsistencies
Incorrect color profiles
Incorrect color profiles often lead to unexpected color results. When the color profile does not match the printer or the materials used, the colors in your prints may appear different from what you intended. This mismatch can cause significant discrepancies between the design and the final output.
Printer calibration issues
Printer calibration issues also contribute to color inconsistencies. If your printer is not properly calibrated, it may not reproduce colors accurately. Calibration ensures that the printer interprets color data correctly, aligning the output with the original design.
Solutions for Color Management
Use of ICC profiles
Using ICC profiles is a crucial step in managing color accuracy. These profiles help standardize the color output across different devices, ensuring that the colors in your prints match the intended design. By applying the correct ICC profiles, you can achieve more consistent and vibrant results.
Regular printer calibration
Regular printer calibration is vital for maintaining color consistency. Calibration adjusts the printer settings to ensure accurate color reproduction. By routinely calibrating your printer, you can prevent color shifts and maintain the quality of your prints.
To enhance your color management efforts, consider utilizing advanced software tools. Programs like Adobe Photoshop and specialized RIP software offer features for fine-tuning color profiles and settings. These tools guide you in maintaining precise color matching, ensuring that your DTF printing projects meet your expectations.
Ink Adhesion and Smudging
In DTF printing, ink adhesion and smudging are common challenges that can affect the quality and durability of your prints. Understanding the causes and implementing effective solutions can help you achieve better results.
Causes of Ink Adhesion Problems
Inadequate curing process
An inadequate curing process often leads to poor ink adhesion. If the ink does not cure properly, it may not bond well with the fabric or film. This can result in the ink flaking off or fading quickly. You need to ensure that the curing process is thorough to maximize ink adhesion.
Poor quality film or fabric
Using poor quality film or fabric can also cause ink adhesion problems. Low-quality materials may not provide a suitable surface for the ink to adhere to, leading to smudging or incomplete transfers. Selecting high-quality materials is crucial for achieving optimal print results.
Solutions for Better Ink Adhesion
Proper curing techniques
Implementing proper curing techniques is essential for enhancing ink adhesion. Adjust the heat and pressure settings during the curing process to ensure that the ink bonds effectively with the substrate. Keeping the printing area clean and controlling humidity can also improve the curing process.
Use of high-quality materials
Choosing high-quality materials significantly impacts ink adhesion. Opt for premium films and fabrics that offer a smooth and receptive surface for the ink. This choice not only improves adhesion but also enhances the overall appearance and longevity of your prints.
Expert Testimony:
“For ink that doesn’t stick or smudges, change the heat, pressure, and ink amount. Also, keep the printing area clean and control the humidity.”
By addressing these issues, you can ensure that your DTF printing projects are vibrant, durable, and of the highest quality. Prioritizing ink adhesion will lead to better print quality and longevity benefits.
Printhead Maintenance and Clogging
In DTF printing, maintaining the printhead is crucial for ensuring smooth operation and high-quality prints. Printhead clogging can disrupt your workflow and lead to poor print results. Understanding the causes and implementing effective maintenance routines can help you avoid these issues.
Causes of Printhead Clogging
Use of low-quality inks
Using low-quality inks often leads to printhead clogging. These inks may contain impurities or inconsistent particle sizes, which can block the tiny nozzles in the printhead. When the nozzles become clogged, the ink flow is restricted, resulting in streaks or incomplete prints. Always choose inks that are specifically designed for your printer model to minimize this risk.
Infrequent printer use
Infrequent use of your printer can also cause printhead clogging. When a printer sits idle for extended periods, the ink in the nozzles can dry up, leading to blockages. Regularly using your printer helps keep the ink flowing and prevents it from drying out. If you don’t use your printer often, consider running a test print or cleaning cycle every few days to maintain the printhead’s condition.
Solutions for Printhead Maintenance
Regular cleaning routines
Implementing regular cleaning routines is essential for maintaining your printhead. Establish a maintenance schedule to check and clean the printhead and surrounding areas. This routine helps ensure there are no obstructions and keeps the printhead in optimal condition. Most printers have built-in cleaning functions that you can use to flush out any dried ink or debris.
Tip: “Implement a routine maintenance schedule to check and clean the printhead and surrounding area, ensuring there are no obstructions.”
Use of recommended inks
Using recommended inks is vital for preventing printhead clogging. Manufacturers design these inks to work seamlessly with specific printer models, ensuring consistent flow and reducing the risk of clogs. By choosing high-quality, compatible inks, you can extend the life of your printhead and maintain the quality of your prints.
By addressing these common causes of printhead clogging and following the recommended maintenance practices, you can ensure that your DTF printing projects run smoothly and produce excellent results. Regular maintenance not only prevents clogs but also enhances the longevity and performance of your printer.
White Ink Challenges
In DTF printing, white ink plays a crucial role as it serves as the base layer for vibrant designs on colored garments. However, it often presents unique challenges that can affect the quality of your prints. Understanding these common issues and their solutions is essential for achieving optimal results.
Common White Ink Issues
Settling and separation
White ink tends to settle and separate over time. This occurs because the pigment in the ink can settle at the bottom of the container, leading to inconsistent ink flow and coverage. If not addressed, this can result in uneven prints and poor opacity.
Inconsistent opacity
Inconsistent opacity is another frequent issue with white ink. When the opacity varies, the white underbase may not adequately cover the fabric, causing the colors to appear dull or washed out. This problem often arises from incorrect printer settings or improper ink mixing.
Solutions for White Ink Problems
Regular ink agitation
To prevent settling and separation, you should regularly agitate the white ink. Shaking the ink bottles thoroughly before use ensures proper mixing and helps maintain consistent ink flow. This simple step can significantly improve the quality of your prints by ensuring even coverage and opacity.
Tip: “Shake the white ink bottles thoroughly before use to ensure proper mixing.”
Adjusting printer settings
Adjusting your printer settings can also help address white ink challenges. Ensure that the print parameters, such as speed and thickness, are correctly set to achieve the desired opacity. Proper calibration of the printer is crucial for maintaining consistent ink application and preventing issues like bleeding or smudging.
By implementing these solutions, you can overcome the common challenges associated with white ink in DTF printing. Regular maintenance and attention to detail will enhance the quality and durability of your prints, ensuring that your designs remain vibrant and eye-catching.
Environmental Factors like Temperature and Humidity
Environmental conditions, such as temperature and humidity, play a significant role in the success of your DTF printing projects. These factors can influence the quality and consistency of your prints, making it essential to understand their impact and how to manage them effectively.
Impact of Environmental Conditions
Temperature fluctuations
Temperature fluctuations can affect the performance of your DTF printer. When temperatures vary widely, they can cause the ink to behave unpredictably, leading to issues like smudging or incomplete transfers. Consistent temperatures help maintain the stability of the ink and ensure smooth operation.
High humidity levels
High humidity levels can also pose challenges in DTF printing. Excess moisture in the air can interfere with the curing process, resulting in poor ink adhesion and smudging. It can also affect the consistency of white ink, leading to uneven prints. Maintaining optimal humidity levels is crucial for achieving high-quality results.
Solutions for Managing Environmental Factors
Controlled printing environment
Creating a controlled printing environment is key to managing temperature and humidity. You should aim to keep your workspace at a stable temperature and humidity level. This control helps prevent fluctuations that can negatively impact your prints. Consider using air conditioning or heating systems to maintain a consistent environment.
Use of dehumidifiers or humidifiers
Using dehumidifiers or humidifiers can help you manage humidity levels effectively. A dehumidifier reduces excess moisture in the air, while a humidifier adds moisture when the air is too dry. By adjusting these devices, you can create an ideal environment for DTF printing, ensuring that your prints are vibrant and durable.
Eco-Friendly Printing:
“Integrated DTF systems not only reduce waste and energy consumption but also offer sustainable solutions by automating processes and minimizing errors.”
By understanding and managing environmental factors, you can enhance the quality and reliability of your DTF printing projects. A stable environment ensures that your prints remain consistent and meet your expectations.
Preventive Maintenance Tips
To keep your DTF printing equipment in top condition, you need to follow preventive maintenance practices. These practices ensure that your printer operates smoothly and produces high-quality prints consistently. By dedicating time to regular maintenance, you can extend the life of your equipment and avoid costly repairs.
Regular Maintenance Practices
Scheduled cleaning and checks
Regular cleaning and checks are essential for maintaining your DTF printer. Set a schedule to clean the printhead, rollers, and other components. This routine helps prevent dust and debris from accumulating, which can lead to clogs and poor print quality. Inspect your printer regularly to identify any potential issues early. Addressing these problems promptly can prevent them from escalating into major repairs.
Use of maintenance kits
Utilizing maintenance kits can simplify the upkeep of your DTF printer. These kits often include cleaning solutions, tools, and replacement parts designed specifically for your printer model. By using these kits, you ensure that you have the right materials on hand for effective maintenance. Follow the manufacturer’s guidelines when using maintenance kits to achieve the best results.
Long-term Care Strategies
Proper storage of materials
Proper storage of materials is crucial for maintaining their quality. Store your inks, films, and other supplies in a cool, dry place away from direct sunlight. This practice prevents degradation and ensures that your materials remain in optimal condition for printing. Check expiration dates regularly and replace any outdated supplies to maintain print quality.
Regular software updates
Keeping your printer’s software up to date is vital for optimal performance. Manufacturers release updates to improve functionality and fix bugs. Regularly check for software updates and install them as needed. These updates can enhance your printer’s capabilities and ensure compatibility with new materials and technologies.
By implementing these preventive maintenance tips, you can ensure that your DTF printing projects run smoothly and produce excellent results. Regular care and attention to detail will help you maintain the quality and reliability of your prints, ultimately leading to a more successful printing experience.
Regular maintenance is crucial for achieving consistent and high-quality results in DTF printing. By understanding common issues and implementing effective solutions, you can ensure reliable print outcomes. Routine tasks like cleaning and calibration prevent equipment failures and extend the lifespan of your printer. Following the manufacturer’s guidelines helps maintain optimal performance. Embrace these practices to enhance your printing experience and produce exceptional prints. Remember, a well-maintained printer not only saves time but also boosts productivity by minimizing downtime.
FAQ
How can I fix ink bleeding in my DTF prints?
To fix ink bleeding, adjust your printer’s ink output to prevent oversaturation. Most DTF printers have settings for controlling ink levels. Ensure you use high-quality, compatible inks to achieve optimal results. Regularly clean the printhead to maintain print quality and prevent clogging.
Why do my DTF prints have washed-out colors?
Washed-out colors often occur when the ink isn’t applied or fused correctly. Adjust the heat and pressure settings on your DTF printer. Allow the ink to dry properly to ensure vibrant colors. Proper drying time and sufficient heat are crucial for clear and vibrant prints.
What causes ink smudging in DTF printing?
Ink smudging can result from improper printer calibration or insufficient drying time. Ensure your printer is calibrated correctly. Allow enough time for the ink to dry before transferring. Adjust curing settings to ensure proper drying and prevent excessive ink application.
How do I prevent printhead clogging?
Prevent printhead clogging by using recommended inks and performing regular maintenance. Clean the printhead and surrounding areas routinely. This practice ensures no obstructions and keeps the printhead in optimal condition. Regular use of the printer also helps prevent ink from drying in the nozzles.
What should I do if my DTF prints show banding?
To fix banding, maintain a clean environment and avoid high humidity. Update your printer’s software and use appropriate paper. Ensure correct color settings and address issues like clogged nozzles and improper ink viscosity. Regular maintenance helps prevent these problems.
How can I improve ink adhesion on my DTF prints?
Improve ink adhesion by using high-quality materials and proper curing techniques. Adjust heat and pressure settings during the curing process. Ensure the printing area is clean and humidity is controlled. These steps enhance ink bonding with the substrate.
What are the common challenges with white ink in DTF printing?
White ink often settles and separates, leading to inconsistent opacity. Regularly agitate the ink to ensure proper mixing. Adjust printer settings to achieve the desired opacity. Proper calibration prevents issues like bleeding or smudging.
How do environmental factors affect DTF printing?
Temperature fluctuations and high humidity can impact print quality. Maintain a stable printing environment with consistent temperature and humidity levels. Use air conditioning or heating systems, and consider dehumidifiers or humidifiers to create an ideal environment for DTF printing.
Why is regular maintenance important for DTF printers?
Regular maintenance prevents common issues and extends the lifespan of your printer. Routine cleaning and checks keep the equipment in top condition. Use maintenance kits for effective upkeep. Proper storage of materials and regular software updates ensure optimal performance.
How can I ensure consistent and high-quality DTF prints?
Ensure consistent and high-quality prints by understanding common issues and implementing effective solutions. Regular maintenance, proper calibration, and using high-quality materials are key. Addressing environmental factors and following preventive maintenance tips enhance print reliability and quality.