
In the world of direct-to-film Powder printing, the debate of PES vs. PA powder can significantly impact your results. PES powder, known for its strong adhesion and wash resistance, excels in high-durability prints on polyester fabrics. It offers excellent color vibrancy, making it a popular choice. On the other hand, PA powder provides a balance between elasticity and durability, making it versatile for various applications. Understanding these differences in the PES vs. PA powder comparison is crucial for selecting the right powder for your specific needs in 2025.
Key Takeaways
PES powder is ideal for high-durability prints on polyester fabrics, offering strong adhesion and excellent wash resistance.
PA powder provides a versatile option, balancing elasticity and durability, making it suitable for nylon and stretchable materials.
When choosing between PES and PA powders, consider the fabric type: PES for polyester and PA for fabrics requiring flexibility.
Sustainability is a growing concern; PA powder generally has a lower environmental impact compared to PES powder.
Stay informed about technological advancements in DTF printing, as innovations in powder formulation and printing technologies are expected to emerge by 2025.
For high-volume production, PES powder ensures consistent quality, while PA powder is better for custom and small batch printing needs.
Understanding the unique properties of each powder can significantly enhance your printing outcomes and help you make informed decisions.
Overview of PES and PA Powders
Understanding the characteristics of PES and PA powders is essential for anyone involved in direct-to-film (DTF) printing. These powders play a crucial role in determining the quality and durability of printed designs.
Definition and Composition
PES Powder
PES powder, or Polyester powder, is a thermoplastic polymer known for its strength and durability. It operates effectively at temperatures ranging from 100 °C to 200 °C. This makes it ideal for applications requiring high-temperature resistance. PES powder provides a rigid finish, which is beneficial for designs that demand strong adhesion and longevity. Its excellent wash resistance ensures that prints maintain their quality over time, even after multiple washes.
PA Powder
PA powder, or Polyamide powder, offers a unique balance between elasticity and durability. It ensures that printed designs adhere well to fabrics while providing a good degree of stretchability. This versatility makes PA powder suitable for various applications, especially where a combination of flexibility and durability is desired. It bridges the gap between the elasticity of TPU and the rigidity of PES, making it a preferred choice for many DTF printing projects.
Historical Context and Evolution
Development of PES Powder
The development of PES powder has been driven by the need for durable and high-temperature-resistant materials in the textile industry. Over the years, advancements in polymer technology have enhanced the performance of PES powders, making them more effective in binding inks to fabrics. This evolution has made PES powders a staple in applications where maximum durability is crucial.
Development of PA Powder
PA powder has evolved to meet the demands for more flexible and versatile printing solutions. Initially developed to provide better adhesion and elasticity, PA powders have undergone significant improvements. These enhancements have expanded their use across various industries, allowing for more creative and durable printing solutions. The balance between elasticity and durability has made PA powders increasingly popular in the DTF printing landscape.
Comparison of Properties
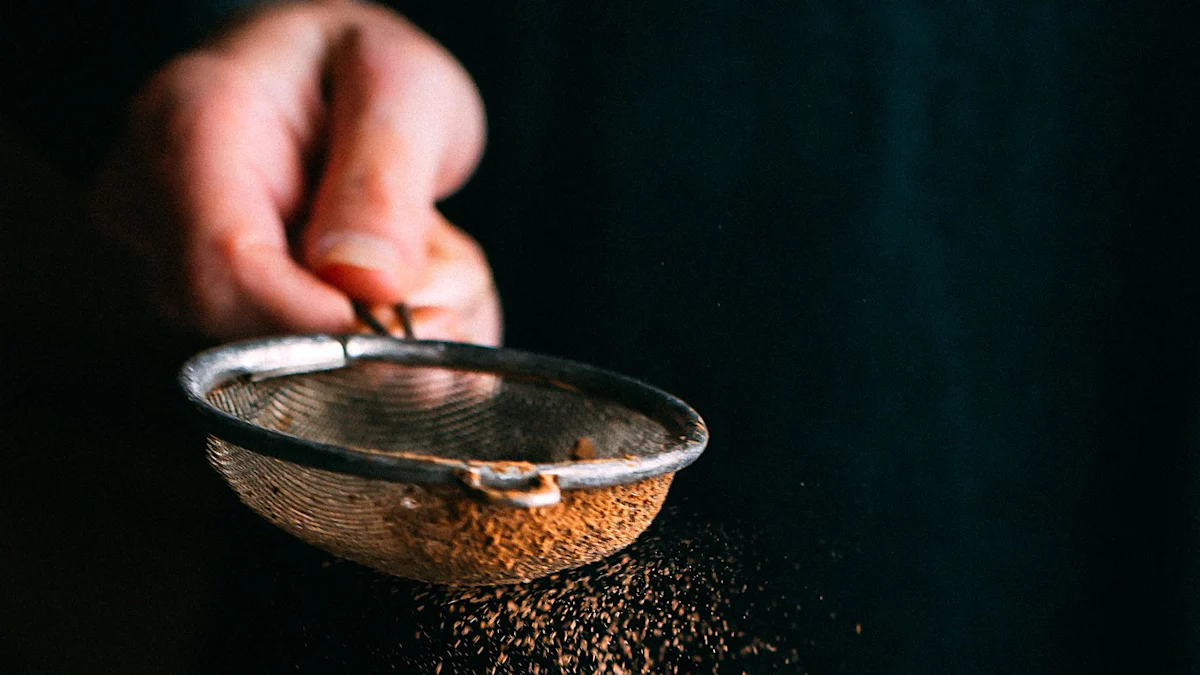
When choosing between PES and PA powders for DTF printing, understanding their properties is crucial. Each powder offers unique characteristics that can significantly impact your printing results.
Physical and Chemical Properties
Durability and Flexibility
PES powder stands out for its durability. It provides a rigid finish, making it ideal for applications where high durability is essential. This rigidity, however, comes at the cost of flexibility. If you prioritize elasticity, PA powder might be more suitable. PA powder offers a balance between elasticity and durability, ensuring good adhesion to fabric while allowing for some stretchability. This makes it versatile for various applications where both flexibility and durability are desired.
Adhesion and Compatibility
Adhesion is a critical factor in DTF printing. PES powder excels in providing strong adhesion, especially on polyester fabrics. Its composition ensures that prints remain intact even after multiple washes. On the other hand, PA powder offers excellent compatibility with a range of fabrics, including nylon. Its ability to adhere well while maintaining flexibility makes it a preferred choice for projects requiring a combination of stretch and durability.
Environmental Impact
Sustainability of PES Powder
Sustainability is becoming increasingly important in the printing industry. PES powder, while known for its durability, poses challenges in terms of environmental impact. The production process involves high energy consumption, and the material itself is not biodegradable. However, ongoing research aims to improve the sustainability of PES powder by developing more eco-friendly formulations.
Sustainability of PA Powder
PA powder offers a more sustainable option compared to PES. Its production process typically consumes less energy, and advancements in polymer technology have led to the development of more environmentally friendly variants. PA powder’s balance of elasticity and durability, combined with its lower environmental footprint, makes it an attractive choice for eco-conscious businesses.
Application Scenarios
When it comes to direct-to-film (DTF) printing, understanding the application scenarios for different powders is crucial. Both PES and PA powders offer unique benefits that cater to specific industry needs and printing requirements.
Industry-Specific Uses
Textile Industry
In the textile industry, choosing the right powder can significantly impact the quality and durability of the final product. PES powder is particularly favored for its strong adhesion and wash resistance, making it ideal for polyester fabrics. This powder ensures that prints remain vibrant and intact even after multiple washes. Its high-temperature resistance also makes it suitable for environments where fabrics are exposed to heat or chemicals. On the other hand, PA powder provides a balance between elasticity and durability, making it versatile for various textile applications. Its ability to adhere well while offering stretchability makes it a preferred choice for fabrics that require flexibility.
Fashion and Apparel
In the fashion and apparel sector, the choice between PES and PA powders can influence the design and functionality of garments. PES powder is often used for clothing items that demand high durability and color vibrancy. It is perfect for polyester-based items, ensuring that designs maintain their quality over time. Meanwhile, PA powder is suitable for fashion pieces that require a combination of flexibility and durability. Its versatility allows designers to create garments that are both stylish and functional, catering to the dynamic needs of the fashion industry.
Suitability for Different Printing Needs
High-Volume Production
For high-volume production, the efficiency and reliability of the powder used in DTF printing are paramount. PES powder stands out in this scenario due to its excellent adhesion properties and durability. It ensures consistent quality across large batches, making it a cost-effective choice for manufacturers. The robust bonding properties of PES powder with polyester fabrics make it suitable for mass production where longevity is crucial.
Custom and Small Batch Printing
Custom and small batch printing requires flexibility and adaptability. PA powder excels in this area due to its balance of elasticity and durability. It allows for creative and unique designs that can adapt to various fabric types. This powder is ideal for projects that require a personalized touch, offering the versatility needed for custom orders. Its compatibility with a range of fabrics, including nylon, makes it a versatile option for small-scale productions.
How PES Powder Works for DTF Printing: Advantages and Applications

Understanding how PES powder functions in the direct-to-film printing process can significantly enhance your printing outcomes. PES powder, or Polyester powder, is a thermoplastic polymer that plays a pivotal role in ensuring high-quality prints. It is renowned for its strong adhesion and wash resistance, making it an excellent choice for high-durability prints.
Benefits of PES Powder in DTF Printing
Strong Adhesion: PES powder excels in providing robust adhesion to fabrics. This characteristic ensures that your designs remain intact and vibrant even after multiple washes. The strong bonding properties make PES powder particularly suitable for sturdier fabrics, where durability is a priority.
Wash Resistance: One of the standout features of PES powder is its exceptional wash resistance. This quality ensures that prints maintain their quality over time, making it ideal for applications where longevity is crucial. You can rely on PES powder to deliver prints that withstand the rigors of frequent washing.
High-Temperature Resistance: PES powder operates effectively at high temperatures, ranging from 100 °C to 200 °C. This makes it suitable for environments where fabrics are exposed to heat or chemicals. The high-temperature resistance ensures that the prints do not degrade under such conditions, maintaining their integrity and appearance.
Color Vibrancy: PES powder contributes to excellent color vibrancy in prints. The powder’s composition allows for vivid and sharp designs, enhancing the overall aesthetic appeal of the printed items. This feature is particularly beneficial in the fashion and apparel industry, where color quality is paramount.
Versatility in Applications: While PES powder is ideal for polyester fabrics, its versatility extends to various applications within the DTF printing process. Whether you are involved in high-volume production or custom and small batch printing, PES powder offers the reliability and quality needed to meet diverse printing requirements.
Incorporating PES powder into your DTF printing process can elevate the quality and durability of your prints. Its strong adhesion, wash resistance, and color vibrancy make it a valuable asset in achieving superior printing results.
How PA Powder Works for DTF Printing: Advantages and Applications
In the realm of direct-to-film printing, understanding how PA powder functions can significantly enhance your printing projects. PA powder, or Polyamide powder, offers a unique blend of elasticity and durability, making it a versatile choice for various applications. This balance ensures that your printed designs adhere well to fabrics while providing a good degree of stretchability.
Benefits of PA Powder in DTF Printing
Elasticity and Durability: PA powder provides an excellent balance between elasticity and durability. This characteristic allows your designs to maintain their integrity while offering flexibility. You can achieve a finish that combines the elasticity of TPU with the rigidity of PES, making it suitable for diverse printing needs.
Versatility: PA powder’s versatility makes it ideal for a wide range of applications. Whether you are working on textiles that require flexibility or need a durable finish, PA powder adapts to your requirements. Its ability to cater to different fabric types enhances its appeal in the printing industry.
Adhesion: Strong adhesion is crucial in DTF printing, and PA powder excels in this area. It ensures that your designs stick firmly to the fabric, maintaining their quality over time. This feature is particularly beneficial for projects that demand both durability and flexibility.
Environmental Considerations: PA powder offers a more sustainable option compared to other powders. Its production process typically consumes less energy, contributing to a lower environmental footprint. This makes PA powder an attractive choice for eco-conscious businesses looking to reduce their impact.
Application Flexibility: The adaptability of PA powder extends to various printing scenarios. Whether you are involved in high-volume production or custom and small batch printing, PA powder provides the reliability and quality needed to meet diverse demands. Its compatibility with a range of fabrics, including nylon, further enhances its utility.
By incorporating PA powder into your DTF printing process, you can achieve prints that are both durable and flexible. Its unique properties make it a valuable asset in producing high-quality, long-lasting designs.
Factors to Consider When Choosing Between PES and PA Powder
When deciding between PES and PA powders for your direct-to-film (DTF) printing needs, you must consider several factors. These considerations will help you select the most suitable powder for your specific applications.
Fabric Type
Polyester Fabrics: If you work with polyester fabrics, PES powder is an excellent choice. It provides strong adhesion and vibrant colors, ensuring your prints remain intact and visually appealing over time. PES powder’s resistance to high temperatures and chemicals makes it ideal for environments where fabrics face such conditions.
Nylon and Stretchable Fabrics: For nylon or fabrics requiring flexibility, PA powder offers a better solution. Its balance of elasticity and durability allows your designs to stretch without compromising quality. This adaptability makes PA powder suitable for various textile applications, especially those demanding both flexibility and strength.
Specialty Fabrics: Consider the unique properties of your fabric. Some specialty materials may require specific powder characteristics. Evaluate the compatibility of PES and PA powders with your fabric type to ensure optimal results.
Business Requirements
Production Volume: Your production volume can influence your choice. PES powder excels in high-volume production due to its consistent quality and durability. It ensures reliable results across large batches, making it cost-effective for manufacturers.
Customization Needs: If your business focuses on custom and small batch printing, PA powder provides the flexibility you need. Its versatility allows for creative designs that adapt to various fabric types, making it ideal for personalized orders.
Environmental Considerations: Sustainability is increasingly important in today’s market. PA powder offers a more eco-friendly option with a lower environmental footprint. If your business prioritizes sustainability, PA powder aligns with your goals by consuming less energy during production.
Durability and Longevity: Consider the durability requirements of your products. PES powder’s strong adhesion and wash resistance make it suitable for items demanding high durability. If longevity is a priority, PES powder ensures your prints withstand frequent washing and wear.
By evaluating these factors, you can make an informed decision between PES and PA powders. Understanding your fabric type and business requirements will guide you in selecting the right powder for your DTF printing projects.
Common Problems When Using PES or PA Powder and How to Solve Them
Troubleshooting Common Issues
When using PES or PA powders in direct-to-film (DTF) printing, you might encounter several common issues. Understanding these problems can help you troubleshoot effectively.
Inconsistent Adhesion: You may notice that prints do not adhere uniformly to the fabric. This often results from incorrect temperature settings or uneven powder application. Ensure that you maintain the recommended temperature range for each powder type. Check your equipment for even distribution of the powder across the film.
Poor Wash Resistance: If prints fade or peel after washing, the issue might lie in the curing process. Insufficient curing time or temperature can weaken the bond between the powder and fabric. Verify that you follow the manufacturer’s guidelines for curing. Adjust the time and temperature settings to enhance wash resistance.
Cracking or Peeling: Cracks or peeling in prints usually indicate a mismatch between the powder and fabric type. PES powder works best with polyester, while PA powder suits nylon and stretchable fabrics. Ensure you select the appropriate powder for your fabric to prevent these issues.
Color Fading: Dull or faded colors can result from improper powder application or low-quality inks. Use high-quality inks compatible with your chosen powder. Ensure even and adequate powder coverage to maintain vibrant colors.
Solutions and Tips
Addressing these common issues requires practical solutions and tips to optimize your DTF printing process.
Temperature and Pressure Settings: Always calibrate your heat press to the correct temperature and pressure settings. This ensures optimal adhesion and prevents issues like peeling or fading.
Powder Application: Apply the powder evenly across the film. Use a sifter or automated applicator for consistent coverage. This step is crucial for achieving uniform adhesion and vibrant prints.
Curing Process: Follow the recommended curing time and temperature for each powder type. Proper curing enhances durability and wash resistance. Consider conducting test prints to fine-tune your settings.
Fabric Compatibility: Match the powder type to the fabric you are using. PES powder is ideal for polyester, while PA powder suits nylon and stretchable materials. This compatibility prevents cracking and ensures long-lasting prints.
Regular Maintenance: Maintain your equipment regularly. Clean your heat press and powder applicator to prevent residue buildup. Regular maintenance ensures consistent performance and print quality.
By addressing these common problems and implementing these solutions, you can enhance the quality and durability of your DTF prints. Understanding the nuances of PES and PA powders will help you achieve optimal results in your printing projects.
Future Trends in 2025
As we look ahead to 2025, the landscape of direct-to-film printing is poised for significant advancements. These changes will shape how you approach printing projects, offering new opportunities and challenges.
Technological Advancements
Innovations in Powder Formulation
In 2025, expect to see groundbreaking innovations in powder formulation. Researchers are exploring new materials that enhance the performance of powders used in DTF printing. These advancements aim to improve adhesion, flexibility, and environmental sustainability. For instance, the integration of biomass composite materials, which include agricultural and forestry remains like wood and straw, could lead to more eco-friendly powders. Such materials not only reduce environmental impact but also offer unique properties that enhance print quality.
Integration with New Printing Technologies
The integration of new printing technologies will revolutionize the DTF printing process. You will likely encounter machines that offer greater precision and efficiency. These advancements will allow for more complex designs and faster production times. As technology evolves, expect to see printers that can seamlessly handle a variety of powders, adapting to different fabric types and printing needs. This integration will enable you to produce high-quality prints with greater ease and consistency.
Market Trends and Predictions
Demand Shifts
The demand for DTF printing is expected to shift significantly by 2025. As consumers become more environmentally conscious, there will be a growing preference for sustainable printing solutions. You may notice an increased demand for eco-friendly powders and printing processes that minimize waste and energy consumption. Additionally, the versatility of DTF printing will attract industries beyond textiles, such as automotive and electronics, further expanding the market.
Emerging Markets
Emerging markets will play a crucial role in the growth of DTF printing. Regions with developing economies are likely to adopt this technology due to its cost-effectiveness and adaptability. You can anticipate a surge in demand from these markets as they seek innovative solutions to meet their printing needs. This expansion will create new opportunities for businesses to tap into previously untapped regions, driving the global growth of DTF printing.
By staying informed about these future trends, you can position yourself to take advantage of the evolving DTF printing landscape. Embracing technological advancements and understanding market shifts will enable you to remain competitive and meet the changing demands of the industry.
In the pes vs. pa powder debate, understanding their differences is crucial for your DTF printing success. PES powder excels in durability and adhesion, making it ideal for polyester fabrics. PA powder offers a balance of elasticity and durability, suitable for nylon and stretchable materials. Choose PES for high-volume, durable prints. Opt for PA when flexibility and sustainability matter. Stay informed about future trends to leverage technological advancements and market shifts. This knowledge ensures you make informed decisions and remain competitive in the evolving printing landscape.
FAQ
What are PES powders used for in DTF printing?
PES powders play a crucial role in DTF printing by binding the ink to the fabric. They offer a more rigid finish compared to TPU, making them suitable for applications that demand higher durability. You will find PES powders ideal for prints on polyester fabrics, providing excellent color vibrancy and adhesion.
What are PA powders used for in DTF printing?
PA powders provide a balance between elasticity and durability in DTF printing. They ensure good adhesion to the fabric while offering stretchability. This makes PA powders suitable for printing on nylon fabrics, often preferred for items like bags and accessories due to their durability.
What is black DTF powder used for?
Black DTF powder is specifically used for black or dark-colored garments. It blocks color migration and provides stretch-resistance, waterproofing, and washability. This ensures that your designs maintain their quality and appearance over time, even on darker fabrics.
How do PES and PA powders differ in terms of fabric compatibility?
PES powders excel on polyester fabrics, offering strong adhesion and vibrant colors. In contrast, PA powders are better suited for nylon and stretchable fabrics, providing a balance of elasticity and durability. Choosing the right powder depends on the fabric type you are working with.
Why is understanding DTF powder properties important?
Understanding DTF powder properties is essential for achieving high-quality printing results. Different powders, like TPU and PES, offer unique benefits tailored for specific applications, such as flexibility, wash resistance, and strong adhesion. Knowing these properties helps you select the right powder for your project.
Can PES and PA powders be used interchangeably?
While PES and PA powders serve similar functions in DTF printing, they are not interchangeable. Each powder has distinct properties that make it suitable for specific fabric types and applications. PES powders are ideal for polyester, while PA powders work best with nylon and stretchable materials.
What are the benefits of using PES powder in DTF printing?
PES powder offers several benefits in DTF printing, including strong adhesion, wash resistance, and high-temperature resistance. It ensures that your prints remain vibrant and intact even after multiple washes, making it an excellent choice for high-durability applications.
What advantages does PA powder offer in DTF printing?
PA powder provides an excellent balance between elasticity and durability. It adapts well to various fabric types, ensuring strong adhesion while allowing for flexibility. This versatility makes PA powder ideal for projects that require both durability and stretchability.
How does black DTF powder enhance print quality on dark garments?
Black DTF powder enhances print quality on dark garments by blocking color migration and providing additional stretch-resistance and waterproofing. This ensures that your designs maintain their integrity and appearance, even on challenging fabric colors.
What should you consider when choosing between PES and PA powders?
When choosing between PES and PA powders, consider factors such as fabric type, production volume, and environmental impact. PES powders are ideal for high-volume production on polyester fabrics, while PA powders offer flexibility and sustainability for custom and small batch printing.